Repairs and Modifications
Hi all,
I've recently picked up the hobby of repairing headphones, bought in job lots or as spares/repairs.
For many of them the repairs have been quite straight-forward, but when it comes to physical damage; it's rarely a simple fix.
Using a 3D Printer however can really help solve many of these mechanical issues that might otherwise condemn a set of headphones to the bin (or ebay for hopefully a bargain price).
The printer I've been using was ~£300 new and has a 300 x 300 x 400mm print volume, which is larger than is usually required. The filament is 1.75mm PLA, extruded in 0.3mm layers, so nothing special in terms of detail resolution but not too painful on print times.
Roccat Khan
The headband for this headset snapped, so I replaced it with a Logitech G Pro headband, printing four adapter pins to make up the difference between the earcup and headband fork sizes.
Logitech G332
On this headset the swivel retaining tabs had broken, so I found a model online for the replacement part. Unfortunately it wasn't quite right, as it was for a similar, but slightly different model. However with some adjustment using a craft knife it was made to fit. I suppose I could have modified the original model to better suit this headset, but since this fix works it wasn't worth spending any more time on what is a fairly budget headset.
Sony MDR-1R
These headphones had one of the ear pads missing, which normally wouldn't be an issue, as cheap replacement ear pads can be found on ebay for almost all popular headphones, including for the MDR-1A/1R. However these particular models use a proprietary plastic ring to clip the pads onto the frames, which was of course also missing and this part cannot be purchased anywhere that I looked. Fortunately I had one of these rings to reference, so after a couple of attempts I was able to print a pair of working replacements.
The original ring is at the top of the picture, with a printed replacement mounted in a new pad on the right. The headphone cups have four clips which slot into the holes in the pad's corners, while the plastic ring itself has two clips on each side. The clip positions are subtly keyed for left and right, so getting these right was a bit of a challenge.
Roland RH-5
One of the forks had snapped at the fork to headband swivel, so I printed a pair of replacements.
One of the advantages of 3D printing is you can make shapes that injection moulding can't, so here the crossover cable can be better retained within fully enclosed tunnels in the fork, rather than the open channels of the original forks.
Google GID5B
This is a bit of an odd one; a pair of noise cancelling bluetooth headphones, manufactured specifically for Google, to supply internally to it's employees. I received them with rotten ear pads and a cracking headband, but otherwise working correctly.
The printed headband still needs some work as its clamping force a little weak, so I'll try a 2.5mm wall thickness, instead of the current 2mm. Also it doesn't pull the bottom of the ear pads in enough, so I'll have to tweak the overall shape somewhat as well.
Razer Kraken X USB
I have a few of these and they all seem to suffer from a broken headband or adjuster arm. For those with broken headbands I modeled up a printable replacement headband. It's non-adjusting, so has to be made specifically for the head size of a specific user, but I feel this is the best option due to how fragile the adjuster arms seem to be at any amount of extension.
The screws are UNC 6-32. I find that this thread is course enough to work well in this kind of printed plastic, so long as the holes are drilled and tapped. They will of course strip if over torqued, but they are much better than an M3, while not being that much bigger (3.6mm vs 3mm diameter) and in my opinion a whole lot better than self tapping screws, as they have a bad habit of splitting the layers apart in printed plastics.
Logitech G35
This one is more of a complete rebuild and a bit of a labour of love, since this was my first proper gaming headset, bought more than a decade ago. After a few years the fork to headband swivels broke on both sides, so with no other recourse I removed the headband entirely and wore the cups under a beanie hat.
The headset's microphone got in the way and the buttons on the side of one of the cups kept getting pressed and pausing/skipping any music being played, so they all had to go. After a while the crossover cable, which was just hanging loose started to fail, so I replaced it with some armoured 2 core, which stood up quite well.
I put up with this arrangement for far too long before eventually moving on and putting them away in a box of junk.
With my recent interest in headphone repair; it would be a shame not to attempt to bring these long neglected workhorses back to life. The headband is from a set of Numskull NS05s, a model with inherent cable issues, making them not worth repairing, but still a source of 50mm drivers, big round ear pads and the aforementioned headband.
The ear cups were covered in that horrible rubberised coating that had gone sticky and needed scouring off.
The nearly three metre USB cable had been run over by my office chair one too many times and had started to fray and kink, while the USB connector had been ripped from the computer at harsh angles to a point where it was deformed, but amazingly still worked. It needed replacing in any case, hence the nice new red cable. Splicing the headphone end of the cable with the short wires coming out of the tiny internal connector (picoblade?) wasn't much fun, but I didn't have crimps for it and definitely didn't have the expensive crimping tool needed either, but it works and ended up quite neat.
If I was to print the forks again I'd bring them in closer to the head, so the headband wasn't quite so expanded and therefore clamped a little less firmly. I had to guess at the final positioning and it looks like I was a bit off from where it should have been. Still an overall success as these headphones are back to being usable again.
The only other thing I'd potentially like to do is add the mic and missing buttons back in, but that relies on finding a donor headset, so I'm not holding my breath.
So that's almost all the things I've done so far that involve combining headphones and 3D Printers. The only other thing I've done will be shown in the DIY forum soon and it's possibly even more ridiculous than the G35 build above.
Thanks for reading.
Hi all,
I've recently picked up the hobby of repairing headphones, bought in job lots or as spares/repairs.
For many of them the repairs have been quite straight-forward, but when it comes to physical damage; it's rarely a simple fix.
Using a 3D Printer however can really help solve many of these mechanical issues that might otherwise condemn a set of headphones to the bin (or ebay for hopefully a bargain price).
The printer I've been using was ~£300 new and has a 300 x 300 x 400mm print volume, which is larger than is usually required. The filament is 1.75mm PLA, extruded in 0.3mm layers, so nothing special in terms of detail resolution but not too painful on print times.
Roccat Khan
The headband for this headset snapped, so I replaced it with a Logitech G Pro headband, printing four adapter pins to make up the difference between the earcup and headband fork sizes.
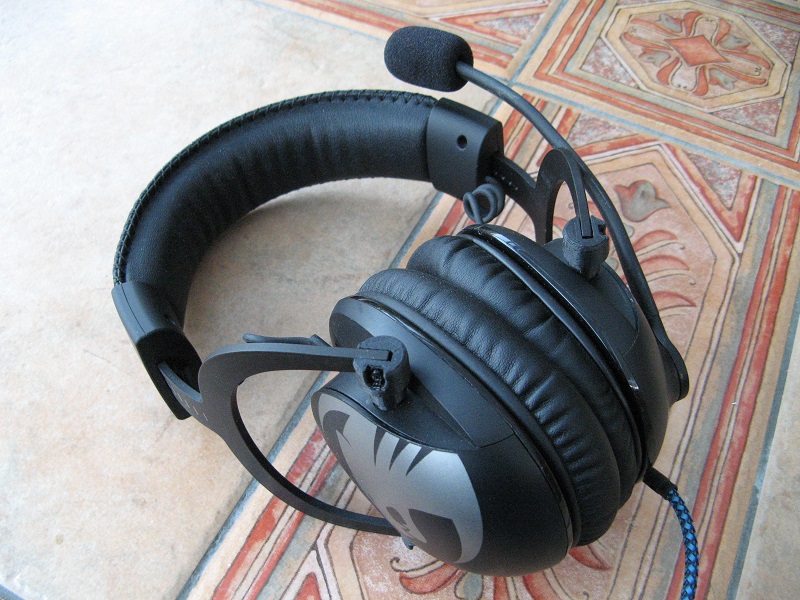
Logitech G332
On this headset the swivel retaining tabs had broken, so I found a model online for the replacement part. Unfortunately it wasn't quite right, as it was for a similar, but slightly different model. However with some adjustment using a craft knife it was made to fit. I suppose I could have modified the original model to better suit this headset, but since this fix works it wasn't worth spending any more time on what is a fairly budget headset.
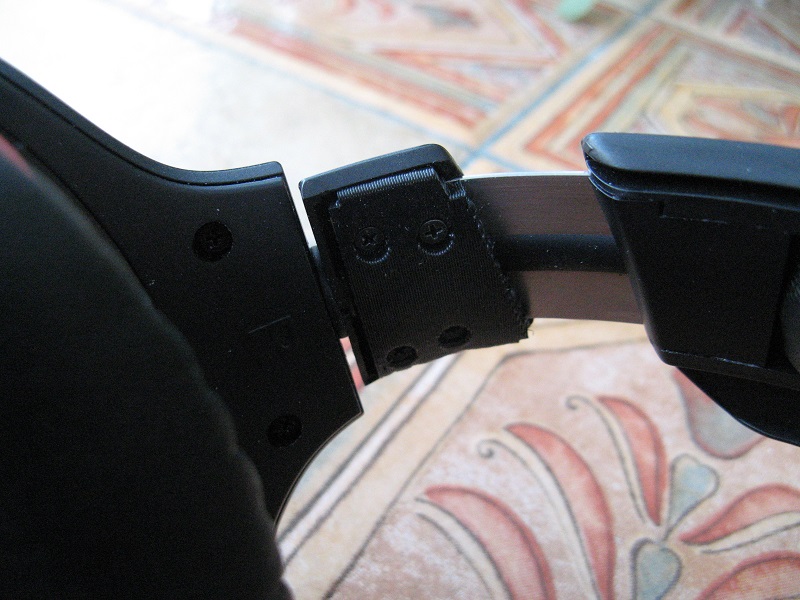
Sony MDR-1R
These headphones had one of the ear pads missing, which normally wouldn't be an issue, as cheap replacement ear pads can be found on ebay for almost all popular headphones, including for the MDR-1A/1R. However these particular models use a proprietary plastic ring to clip the pads onto the frames, which was of course also missing and this part cannot be purchased anywhere that I looked. Fortunately I had one of these rings to reference, so after a couple of attempts I was able to print a pair of working replacements.
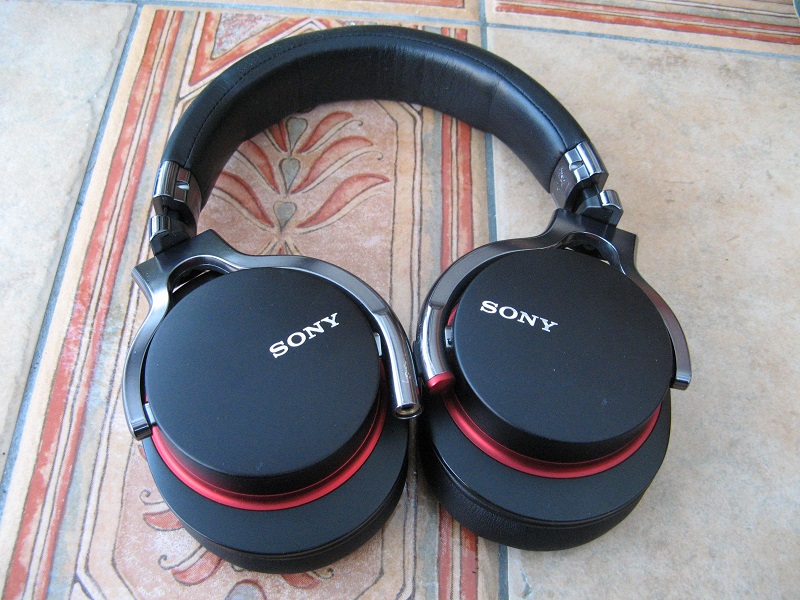
The original ring is at the top of the picture, with a printed replacement mounted in a new pad on the right. The headphone cups have four clips which slot into the holes in the pad's corners, while the plastic ring itself has two clips on each side. The clip positions are subtly keyed for left and right, so getting these right was a bit of a challenge.
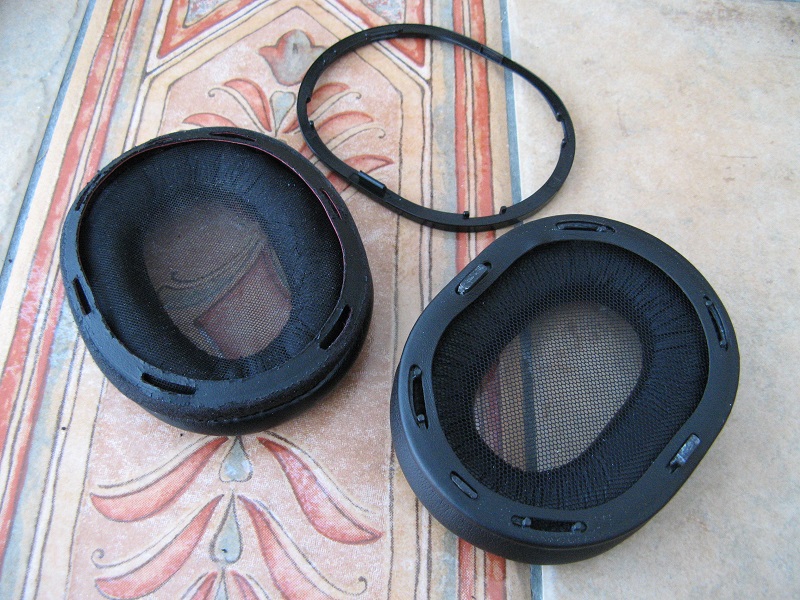
Roland RH-5
One of the forks had snapped at the fork to headband swivel, so I printed a pair of replacements.
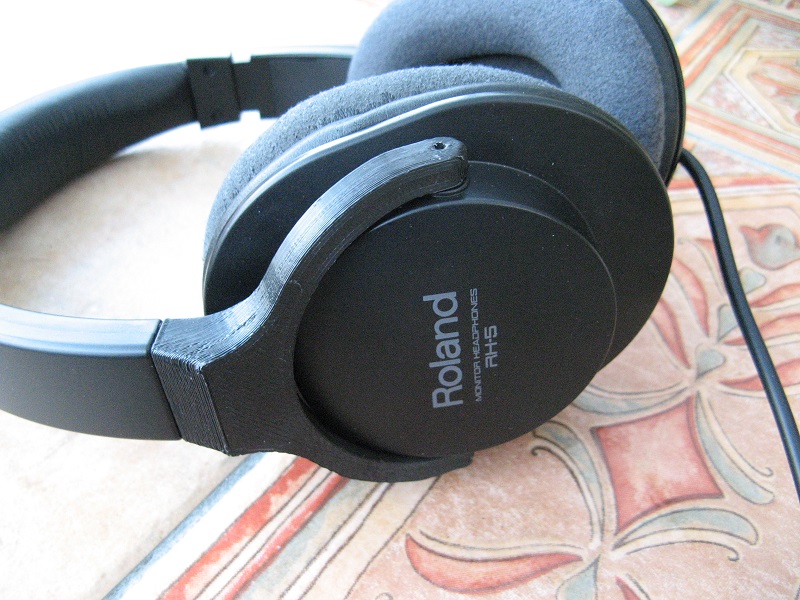
One of the advantages of 3D printing is you can make shapes that injection moulding can't, so here the crossover cable can be better retained within fully enclosed tunnels in the fork, rather than the open channels of the original forks.
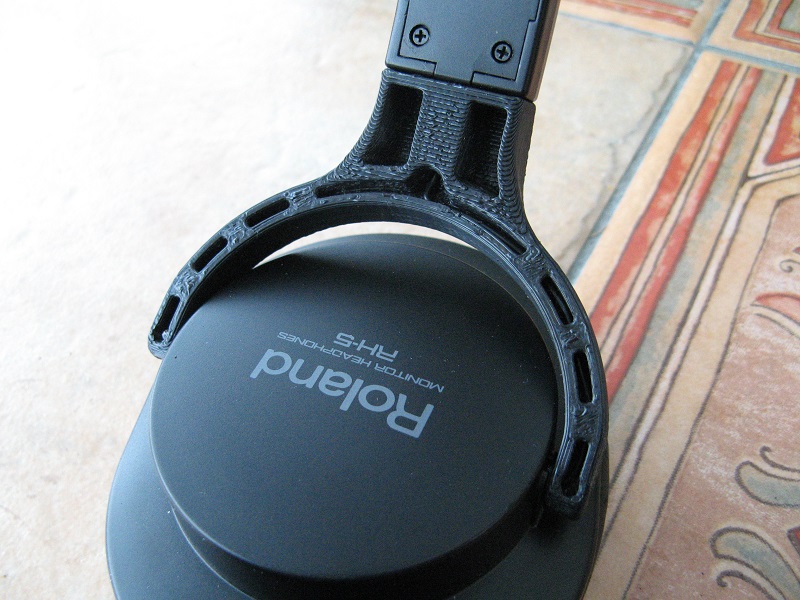
Google GID5B
This is a bit of an odd one; a pair of noise cancelling bluetooth headphones, manufactured specifically for Google, to supply internally to it's employees. I received them with rotten ear pads and a cracking headband, but otherwise working correctly.
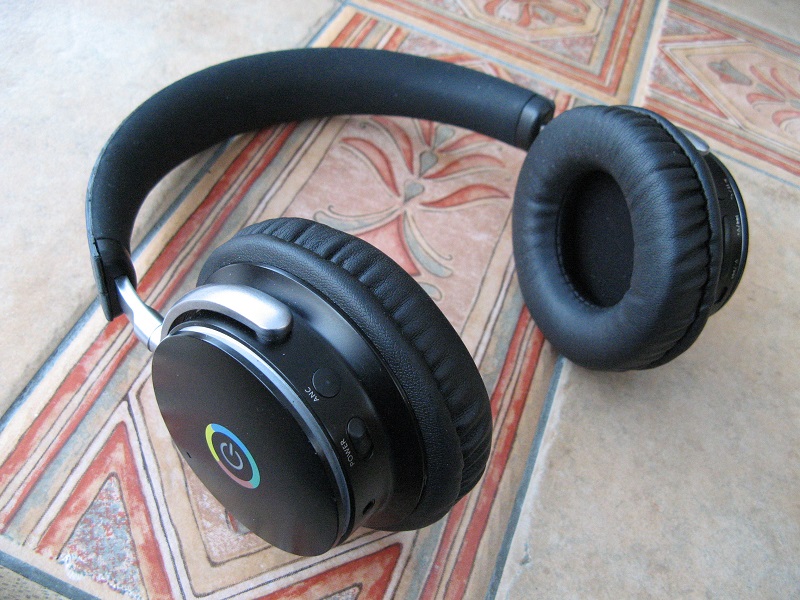
The printed headband still needs some work as its clamping force a little weak, so I'll try a 2.5mm wall thickness, instead of the current 2mm. Also it doesn't pull the bottom of the ear pads in enough, so I'll have to tweak the overall shape somewhat as well.
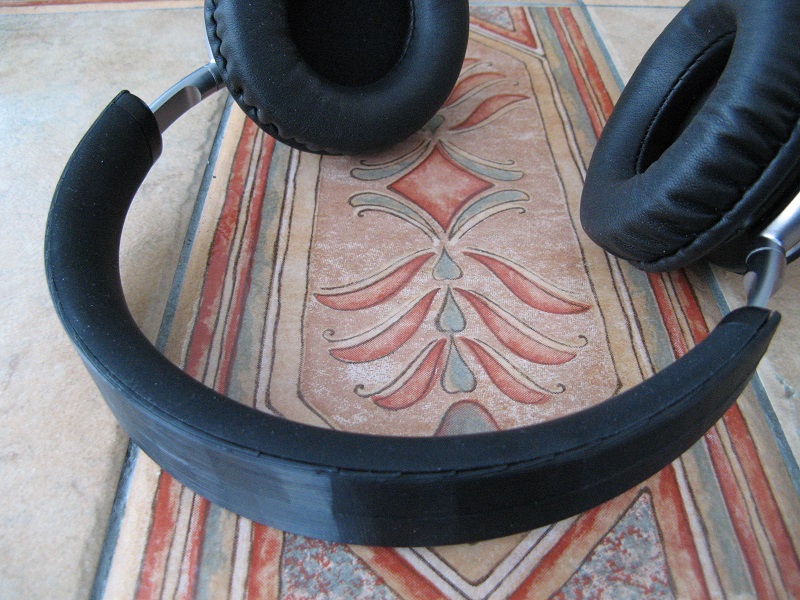
Razer Kraken X USB
I have a few of these and they all seem to suffer from a broken headband or adjuster arm. For those with broken headbands I modeled up a printable replacement headband. It's non-adjusting, so has to be made specifically for the head size of a specific user, but I feel this is the best option due to how fragile the adjuster arms seem to be at any amount of extension.
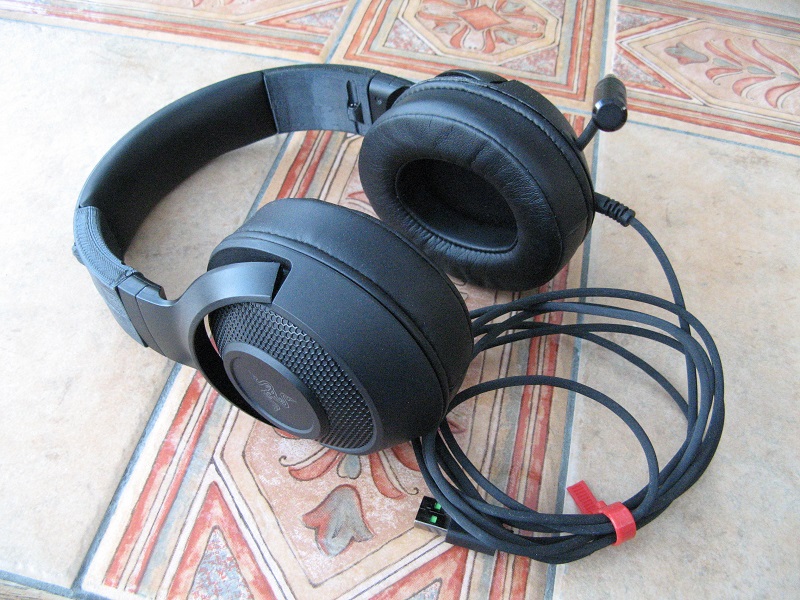
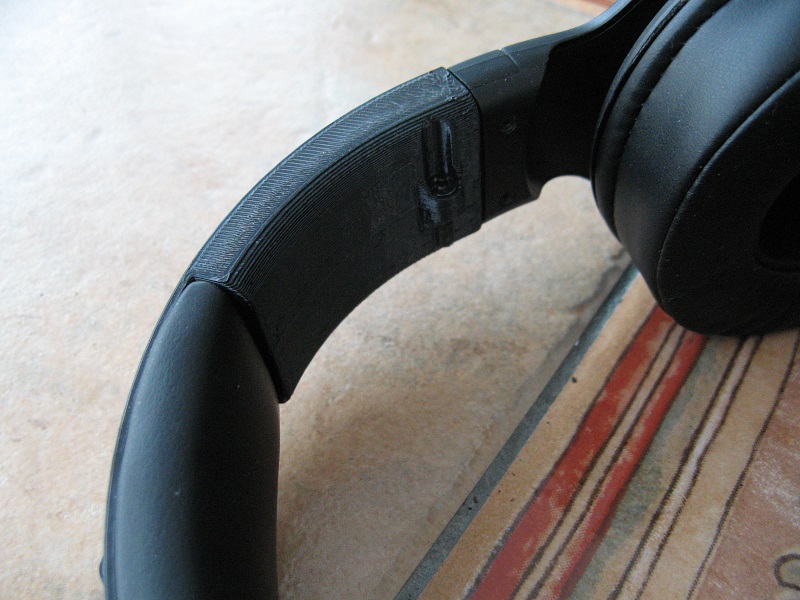
The screws are UNC 6-32. I find that this thread is course enough to work well in this kind of printed plastic, so long as the holes are drilled and tapped. They will of course strip if over torqued, but they are much better than an M3, while not being that much bigger (3.6mm vs 3mm diameter) and in my opinion a whole lot better than self tapping screws, as they have a bad habit of splitting the layers apart in printed plastics.
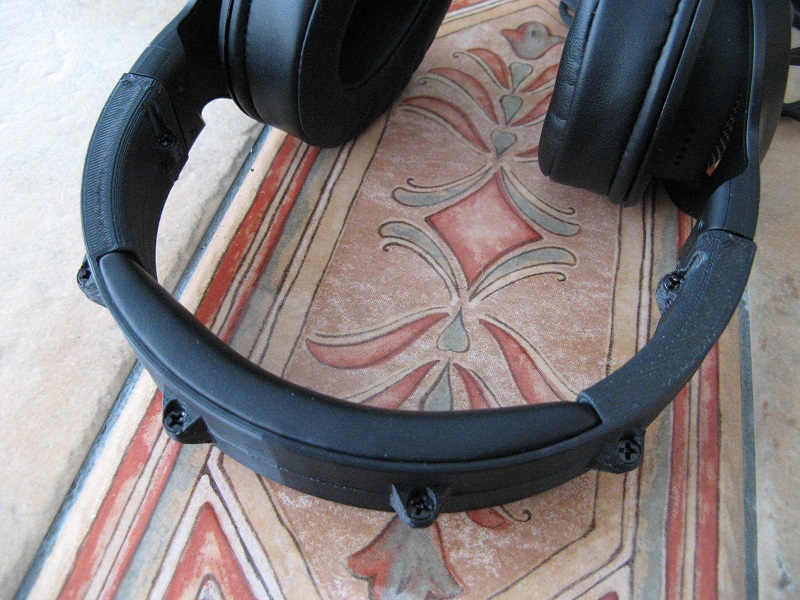
Logitech G35
This one is more of a complete rebuild and a bit of a labour of love, since this was my first proper gaming headset, bought more than a decade ago. After a few years the fork to headband swivels broke on both sides, so with no other recourse I removed the headband entirely and wore the cups under a beanie hat.
The headset's microphone got in the way and the buttons on the side of one of the cups kept getting pressed and pausing/skipping any music being played, so they all had to go. After a while the crossover cable, which was just hanging loose started to fail, so I replaced it with some armoured 2 core, which stood up quite well.
I put up with this arrangement for far too long before eventually moving on and putting them away in a box of junk.
With my recent interest in headphone repair; it would be a shame not to attempt to bring these long neglected workhorses back to life. The headband is from a set of Numskull NS05s, a model with inherent cable issues, making them not worth repairing, but still a source of 50mm drivers, big round ear pads and the aforementioned headband.
The ear cups were covered in that horrible rubberised coating that had gone sticky and needed scouring off.
The nearly three metre USB cable had been run over by my office chair one too many times and had started to fray and kink, while the USB connector had been ripped from the computer at harsh angles to a point where it was deformed, but amazingly still worked. It needed replacing in any case, hence the nice new red cable. Splicing the headphone end of the cable with the short wires coming out of the tiny internal connector (picoblade?) wasn't much fun, but I didn't have crimps for it and definitely didn't have the expensive crimping tool needed either, but it works and ended up quite neat.
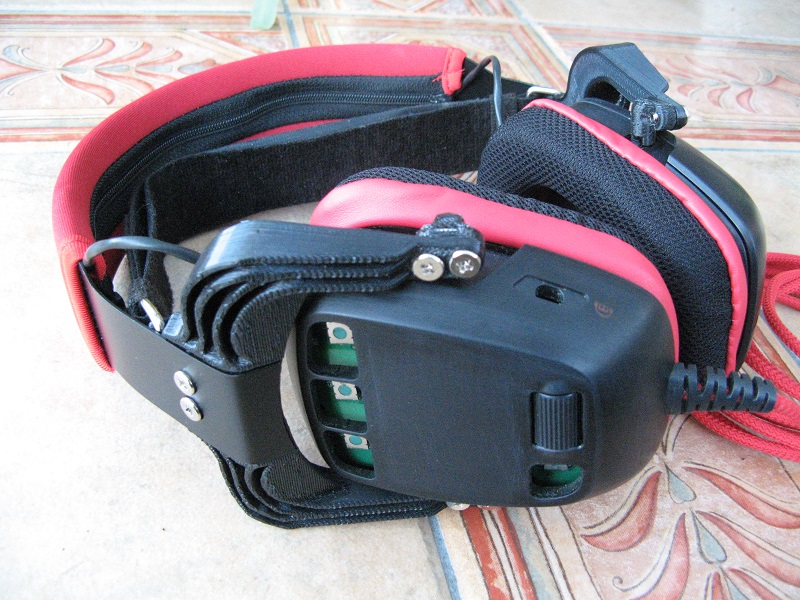
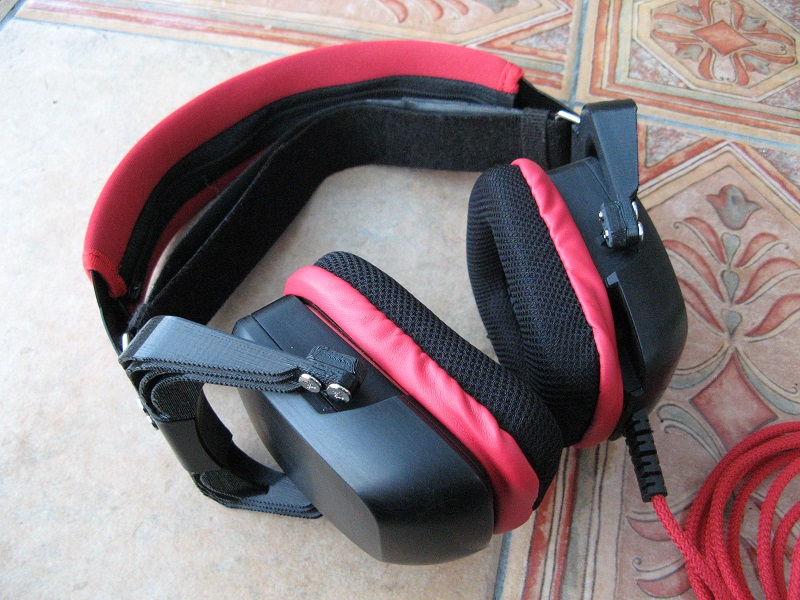
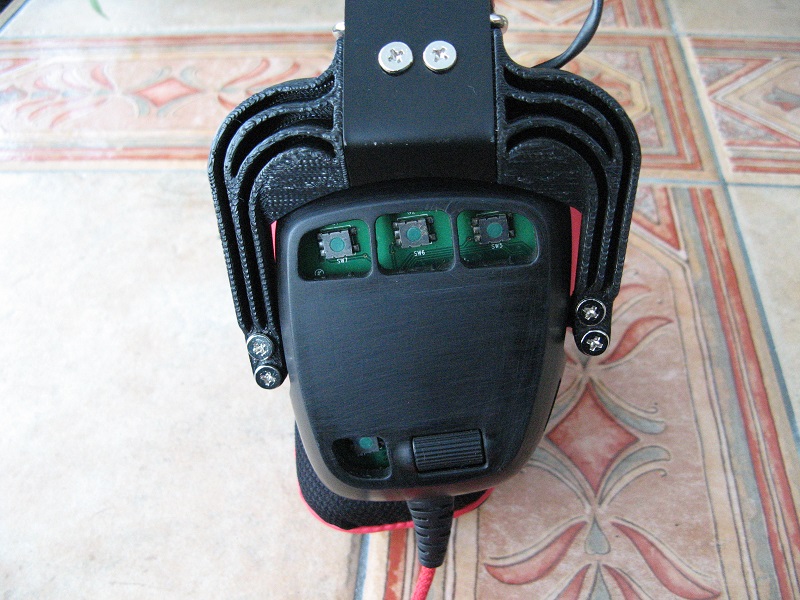
If I was to print the forks again I'd bring them in closer to the head, so the headband wasn't quite so expanded and therefore clamped a little less firmly. I had to guess at the final positioning and it looks like I was a bit off from where it should have been. Still an overall success as these headphones are back to being usable again.
The only other thing I'd potentially like to do is add the mic and missing buttons back in, but that relies on finding a donor headset, so I'm not holding my breath.
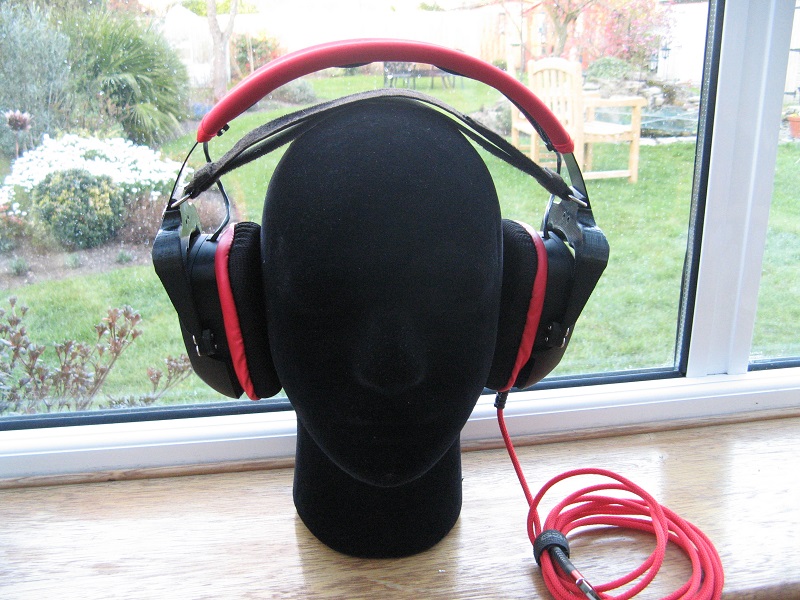
So that's almost all the things I've done so far that involve combining headphones and 3D Printers. The only other thing I've done will be shown in the DIY forum soon and it's possibly even more ridiculous than the G35 build above.
Thanks for reading.
Last edited: